Metal ürünleri kişiselleştirirken doğru işleme yöntemini seçmek, ürünün kalitesi, maliyeti ve teslimat süresi açısından kritik öneme sahiptir. Metalleri kişiselleştirmenin çeşitli yaygın yöntemleri vardır.Yaygın olarak kullanılan birkaç metal özelleştirme yöntemi şunlardır:
1.CNC İşleme:
CNC (Bilgisayar Sayısal Kontrolü) işleme, bilgisayar kontrollü takım tezgahları kullanılarak hassas metal kesme ve işleme yöntemidir.CNC işleme, önceden programlanmış talimatları kullanarak, karmaşık şekillere ve kesin gereksinimlere sahip ürünler için uygun olan metal parçaların yüksek hassasiyette ve verimli şekilde özelleştirilmesini sağlar.
Avantajları:
Yüksek hassasiyet ve doğruluk
Geniş uyumlu malzeme yelpazesi
Karmaşık şekiller ve karmaşık tasarımlar için uygundur
Hem küçük hem de büyük üretim süreçleri için verimli
Dezavantajları:
Daha yüksek ilk kurulum maliyeti
Karmaşık tasarımlar için daha uzun üretim süresi
Çıkarıcı üretimle sınırlıdır (malzeme çıkarma)
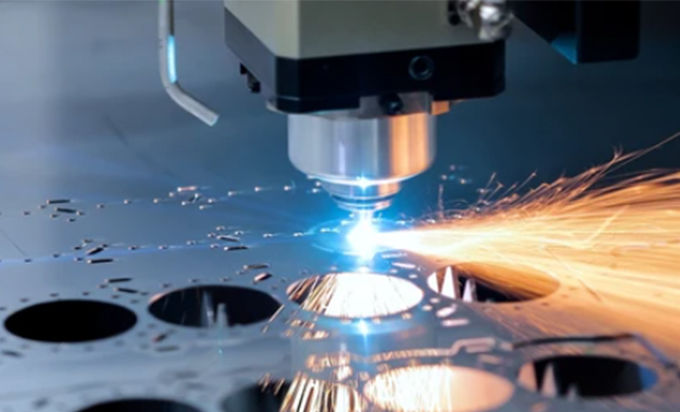
2.Frezeleme ve Tornalama:
Frezeleme ve tornalama, özelleştirilmiş şekil ve boyutlar elde etmek için işleme ekipmanındaki takımları kullanarak metal malzemenin iş parçalarından kesilmesini içerir.Frezeleme düz ve karmaşık yüzey işleme için uygundur, tornalama ise silindirik iş parçaları için kullanılır.
Avantajları:
Hassas ve doğru işleme
Çeşitli şekil ve boyutlar için çok yönlü
Hem prototiplere hem de büyük ölçekli üretime uygundur
Geniş uyumlu malzeme yelpazesi
Dezavantajları:
Karmaşık tasarımlar için daha uzun işleme süresi
Daha yüksek ekipman ve bakım maliyetleri
Tornalamada dönel veya simetrik parçalarla sınırlıdır
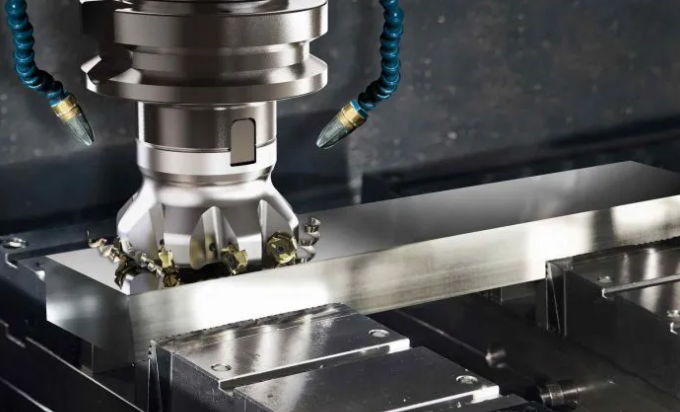
3.3D Baskı:
3D baskı teknolojisi, malzemelerin katman katman biriktirilmesiyle metal parçaların özelleştirilmesini sağlar.Metal tozlarının eritilmesi veya katılaştırılmasıyla karmaşık şekilli metal parçalara doğrudan baskı yapılabilir; bu da hız, esneklik ve kişiselleştirme avantajları sunar.
Avantajları:
Son derece özelleştirilebilir ve karmaşık tasarımlar
Hızlı prototipleme ve azaltılmış teslim süresi
Geleneksel yöntemlere göre daha az malzeme israfı
Düşük adetli üretime uygun
Dezavantajları:
Geleneksel yöntemlere göre sınırlı malzeme seçeneği
Bazı geleneksel yöntemlere kıyasla daha düşük güç ve dayanıklılık
Daha büyük parçalar için daha yavaş üretim hızı
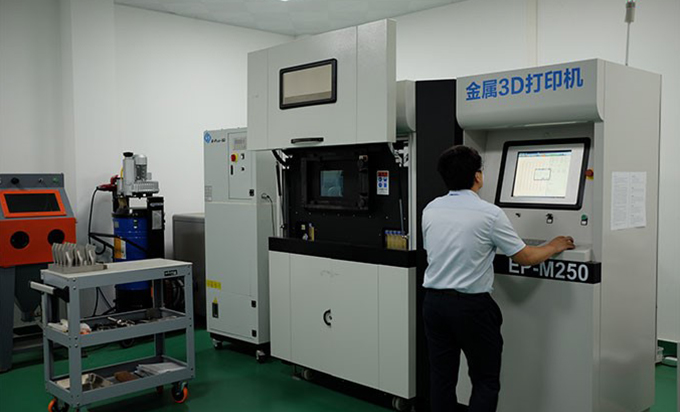
4.Lazer Kesim:
Lazer kesim, metal malzemeleri kesme amacıyla eritmek, buharlaştırmak veya yakmak için yüksek enerjili lazer ışınını kullanan bir yöntemdir.Lazer kesim, yüksek hassasiyet, hız, temassız ve minimum deformasyon gibi avantajlar sunarak çok çeşitli metal parçaların ve yapıların özelleştirilmesi için uygun hale getirir.
Avantajları:
Yüksek hassasiyet ve ince detay
Hızlı kesme hızı
Temassız işlem, malzeme bozulmasını en aza indirir
Çeşitli metaller ve kalınlıklar için uygundur
Dezavantajları:
2D kesme profilleriyle sınırlıdır
Daha yüksek ekipman ve bakım maliyetleri
Pürüzsüz kenarlar için ek son işlem gerektirebilir
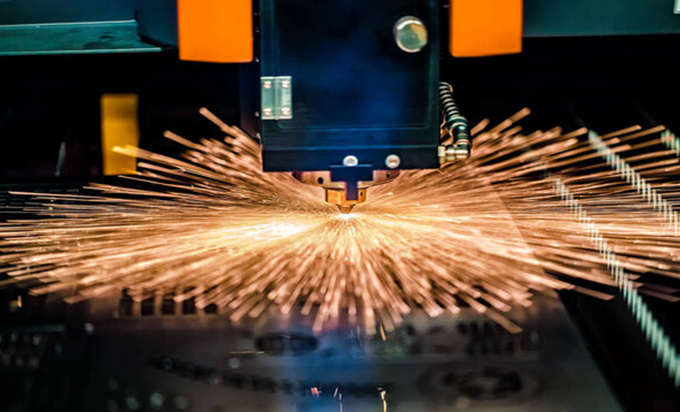
5.Damgalamave Şekillendirme:
Damgalama ve şekillendirme, metal malzemelere istenilen formları vermek için basınç uygulanmasını içerir.Karmaşık şekillere ve yüksek hassasiyete sahip özel metal parçalar ve bileşenler elde etmek için soğuk damgalama veya sıcak damgalama işlemleri kullanılabilir.
Avantajları:
Büyük miktarlar için yüksek üretim hızı
Tekrarlanan tasarımlar için uygun maliyetli
Karmaşık şekiller ve dar toleranslar için uygundur
Geliştirilmiş malzeme gücü ve dayanıklılık
Dezavantajları:
Daha yüksek ilk takım maliyeti
Belirli şekil ve boyutlarla sınırlıdır
Prototipler veya küçük üretim çalışmaları için ideal değildir
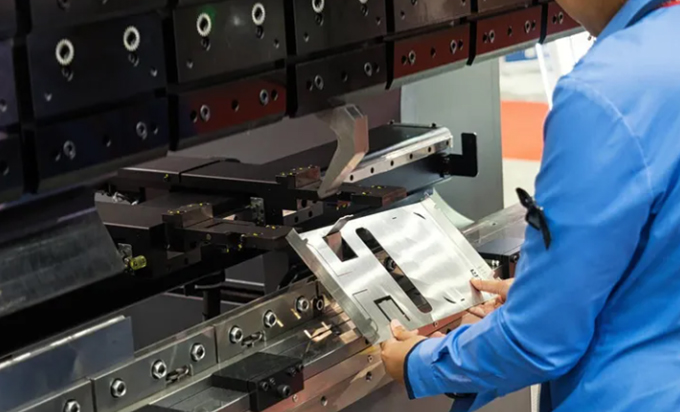
6.Döküm:
Basınçlı Döküm, erimiş metalin yüksek basınç altında bir kalıba enjekte edilerek hızla katılaşıp istenen şekli oluşturduğu bir işlemdir.Ana adımlar kalıp hazırlama, metal eritme, enjeksiyon, soğutma ve kalıptan çıkarma işlemlerini içerir.
Avantajları:
Yüksek Hassasiyet: Basınçlı Döküm, tutarlılık ve yüksek doğruluk sağlayarak karmaşık şekillere, karmaşık ayrıntılara ve hassas boyutlara sahip parçalar üretebilir.
Yüksek Üretim Verimliliği: Basınçlı Döküm seri üretime uygundur, hızlı enjeksiyon ve hızlı soğutma ile yüksek çıktı oranları sağlar.
Mukavemet ve Dayanıklılık: Döküm parçalar tipik olarak yüksek mukavemet, sertlik ve korozyon direnci dahil olmak üzere mükemmel mekanik özellikler sergiler.
Dezavantajları:
Yüksek Maliyet: Basınçlı Döküm, özel metal kalıpların üretimini gerektirir; bu, kalıp üretimi ve hazırlama maliyetleri açısından pahalı olabilir.
Sınırlı Malzeme Seçimi: Basınçlı Döküm öncelikle alüminyum alaşımları, çinko alaşımları ve magnezyum alaşımları gibi düşük erime noktalı metallere uygulanabilir.Çelik veya bakır gibi yüksek erime noktasına sahip metaller için daha az uygundur.
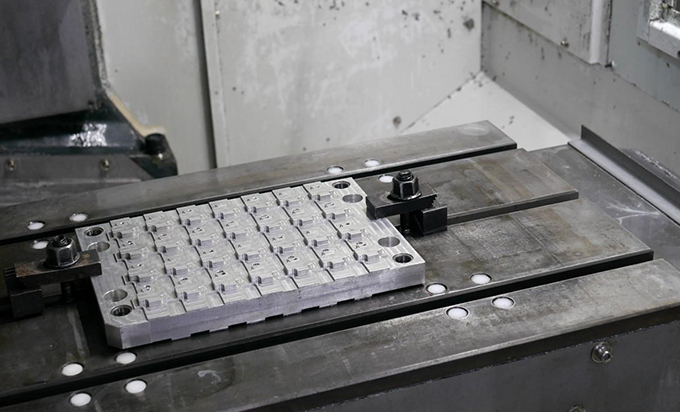
7.Ekstrüzyon:
Ekstrüzyon, ısıtılmış metalin, sürekli kesit şekilleri oluşturmak üzere bir ekstrüzyon makinesi kullanılarak bir kalıptan geçirildiği bir işlemdir.Ana adımlar metal kütüğün ön ısıtılmasını, ekstrüzyon, soğutma ve kesmeyi içerir.
Avantajları:
Verimli Üretim: Ekstrüzyon, sürekli üretime uygundur ve uzun parçaların ve büyük miktarlarda parçaların hızlı ve verimli bir şekilde üretilmesini sağlar.
Çok Yönlü Şekiller: Ekstrüzyon, katı, içi boş ve karmaşık profiller gibi çeşitli kesit şekilleri üretmek için kullanılabilir ve yüksek düzeyde uyarlanabilirlik sunar.
Malzeme Tasarrufu: Ekstrüzyon kalıbının şekli ve boyutlarının kontrolü sayesinde malzeme israfı en aza indirilebilir.
Dezavantajları:
Sınırlı Hassasiyet: Basınçlı Döküm ile karşılaştırıldığında Ekstrüzyon daha düşük hassasiyete ve daha yüksek yüzey pürüzlülüğüne sahiptir.
Malzeme Sınırlamaları: Ekstrüzyon öncelikle alüminyum ve bakır gibi dövülebilir metaller için uygundur.Daha sert metaller için durum daha da zorlaşır.
Kalıp İmalatı: Ekstrüzyon kalıplarının üretimi ve bakımı özel beceriler gerektirir ve daha yüksek maliyetlere neden olur.
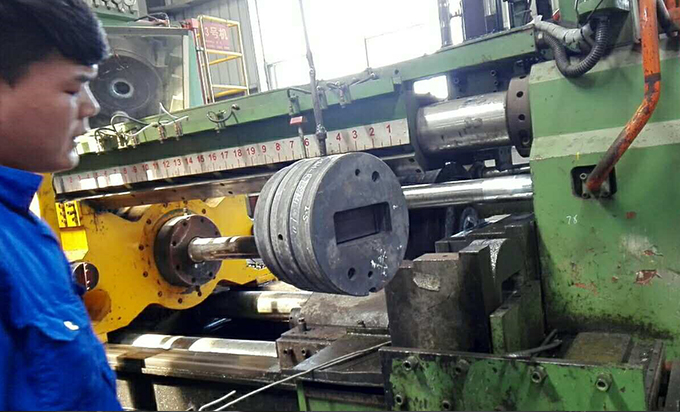
Doğru özel metal işleme yöntemi nasıl seçilir
Ürün tasarımı ve gereksinimleri: Ürünün şekil, boyutlar, malzeme ve yüzey gereksinimleri dahil tasarım gereksinimlerini anlayın.Farklı ürün tasarımları ve gereksinimleri için farklı metal işleme yöntemleri uygundur.
Malzeme seçimi: Ürünün özelliklerine ve gereksinimlerine göre uygun metal malzemeyi seçin.Farklı metal malzemeler farklı işleme yöntemlerine uygundur.Örneğin alüminyum alaşımları ekstrüzyon ve basınçlı döküm için uygundur, paslanmaz çelik ise CNC işleme ve döküm için uygundur.
İşleme hassasiyeti: Ürünün hassasiyet gereksinimlerine göre uygun işleme yöntemini seçin.CNC işleme ve taşlama gibi bazı yöntemler, yüksek doğruluk gerektiren ürünler için uygun olan, daha yüksek hassasiyet ve yüzey kalitesi sağlayabilmektedir.
Üretim hacmi ve verimliliği: Ürünün üretim hacmini ve verimlilik gereksinimlerini göz önünde bulundurun.Büyük ölçekli üretim için damgalama, ekstrüzyon ve basınçlı döküm gibi yüksek verimli işleme yöntemleri daha uygun olabilir.Küçük seri üretim veya özelleştirilmiş ürünler için CNC işleme ve 3D baskı gibi yöntemler esneklik sunar.
Maliyet hususları: Ekipman yatırımı, süreç akışı ve malzeme maliyetleri dahil olmak üzere işleme yönteminin maliyet faktörlerini hesaba katın.Farklı işleme yöntemlerinin farklı maliyet yapıları vardır, dolayısıyla maliyet etkinliği dikkate alınmalıdır.
Profesyonel mühendislerden oluşan ekibimiz, çok çeşitli metal işleme yöntemlerinde oldukça bilgilidir ve size değerli bilgiler ve öneriler sağlayabilir.Sektördeki en son gelişmeler hakkında derinlemesine bilgi sahibiyiz ve özel projeniz için en uygun yöntemi seçmenin karmaşıklıklarını aşmanıza yardımcı olabiliriz.
Hassas işleme, dövme, döküm veya başka herhangi bir metal işleme tekniği konusunda yardıma ihtiyacınız olsun, mühendislerimiz gereksinimlerinize uygun rehberlik sunabilir.Bilgili bir karar vermenize yardımcı olmak için malzeme özellikleri, istenilen toleranslar, üretim hacmi ve maliyet hususları gibi faktörleri dikkate alacağız.
Ek olarak mühendislerimiz, metal bileşenlerinizin tasarımını üretilebilirlik açısından optimize etme konusunda destek sağlayabilir ve bunların seçilen işleme yöntemi kullanılarak verimli bir şekilde üretilebilmesini sağlayabilir.Ürünlerinizin genel kalitesini, işlevselliğini ve maliyet etkinliğini iyileştirebilecek tasarım değişiklikleri için öneriler sunabiliriz.
Lütfen benimle iletişime geçmekten çekinmeyin; metal işlemenizde en iyi sonuçları elde etmenize yardımcı olmaya hazırız.
Gönderim zamanı: 18 Aralık 2023